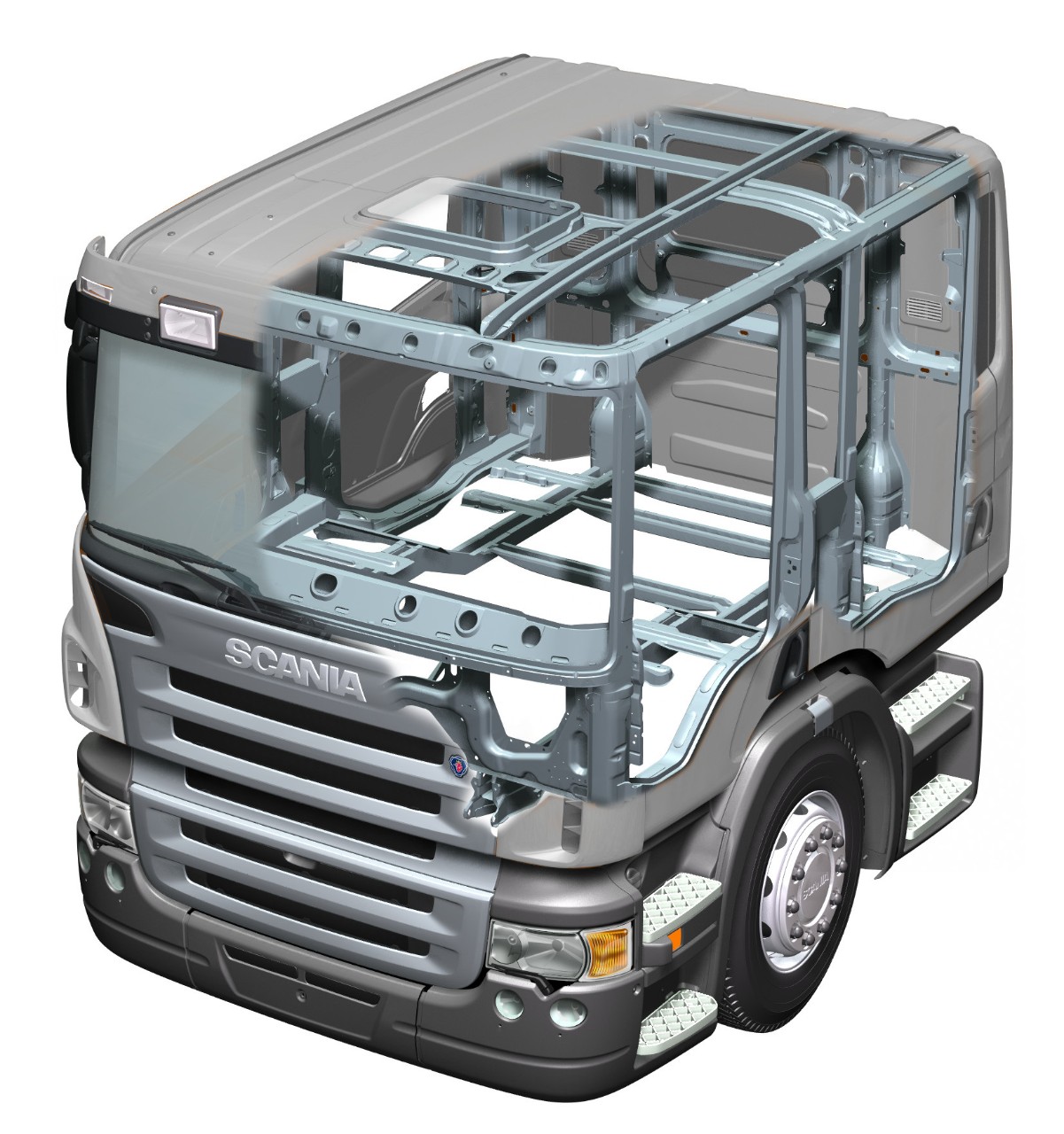
Engine speed control using CAN
Selection
Description
With this function, the engine speed can be controlled from outside the cab by using a CAN message from an external control unit.
Suitable for applications such as:
- Fire engines
- Concrete mixer trucks
- Concrete pump trucks
Connecting CAN Signals
C493-3
Connect the bodywork function to low external CAN signal via harness-to-harness connector C493, pin 3.
C493-4
Connect the bodywork function to low external CAN signal via harness-to-harness connector C493, pin 4.
Function
To be able to increase or decrease the engine speed, the correct CAN messages according to protocol J1939 must be sent to the control unit for the electrical interface (BCI, Bodywork Communication Interface).
The following logic diagram makes it possible to use CAN messages to control the engine speed from outside the cab. When the EXT switch is activated and the power take-off is engaged, engine speed 1 will be activated.
Note: The EK power take-off shown in this logic diagram is only an example. All types of power take-offs can be connected. The Engine speed 1 parameter must be adjusted in Scania’s programming tool for bodybuilders (SDP3), as shown in the illustration below.
|
||
To be able to receive the signals outside the cab, it is suitable to connect a cable harness for bodywork functions to harness-to-harness connector C494. The cable harness is distributed to the 3 DIN harness-to-harness connectors C486, C487 and C488.
More information is found in the following documents: